Ericsson Master Clock
30 June 2024
This is a 1950s Ericsson master clock (yes, that Ericsson!) with a Swiss Moser-Baer movement. It has connections for a bipolar secondary clock circuit and a bell circuit, which can be programmed up to every five minutes with separate programs for weekdays and weekends.

The clock arrived from eBay Germany from a collector’s estate. Though it was missing the pendulum and has quite a few signs of wear, I was drawn to it instantly for its clever mechanism, carefully-arranged wiring, shadow-box-like case, and the lovely etched glass. The original dial is also great in a utilitarian sort of way, but from the beginning I had no intention of using it, since it hides all the best bits.
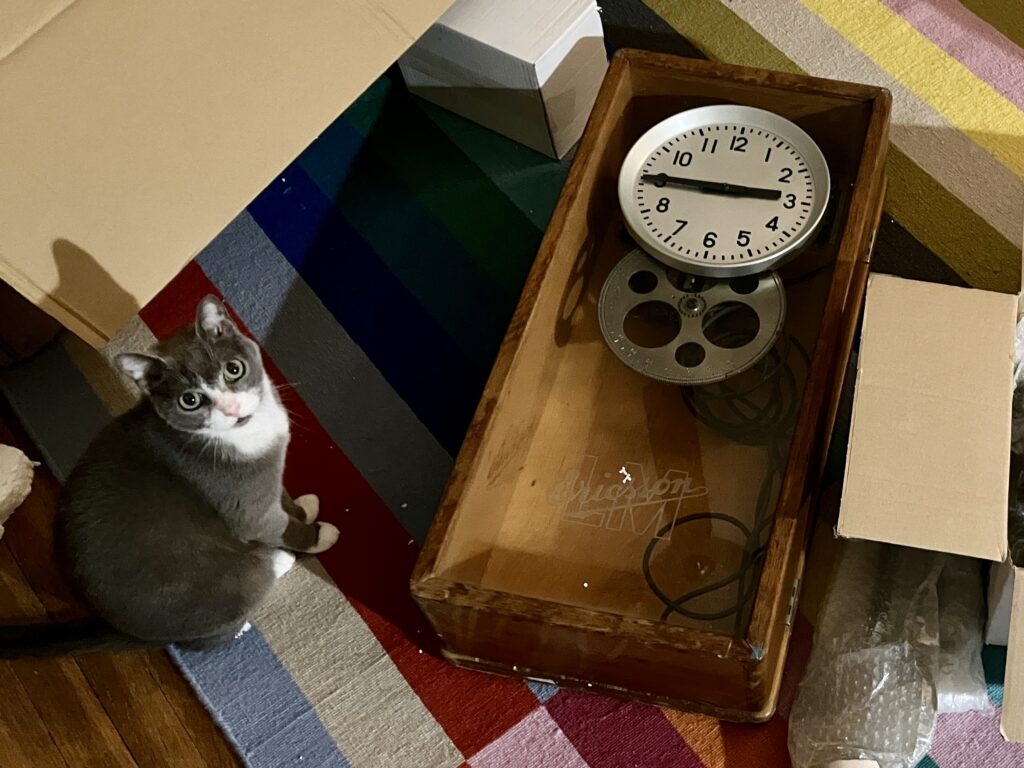
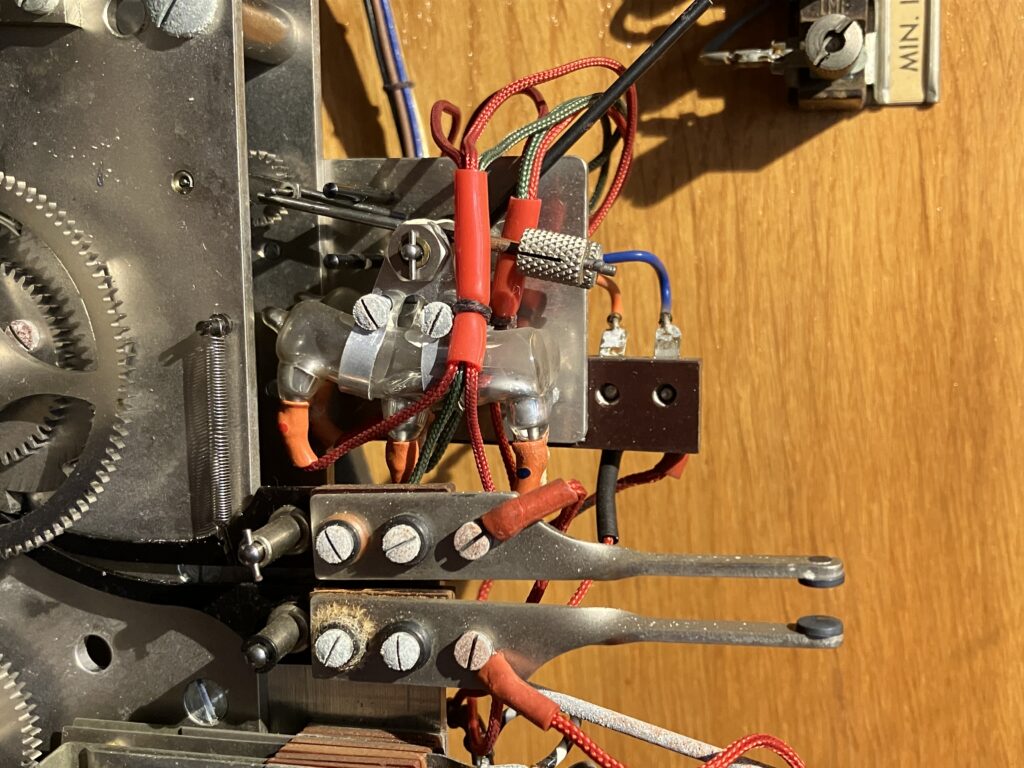
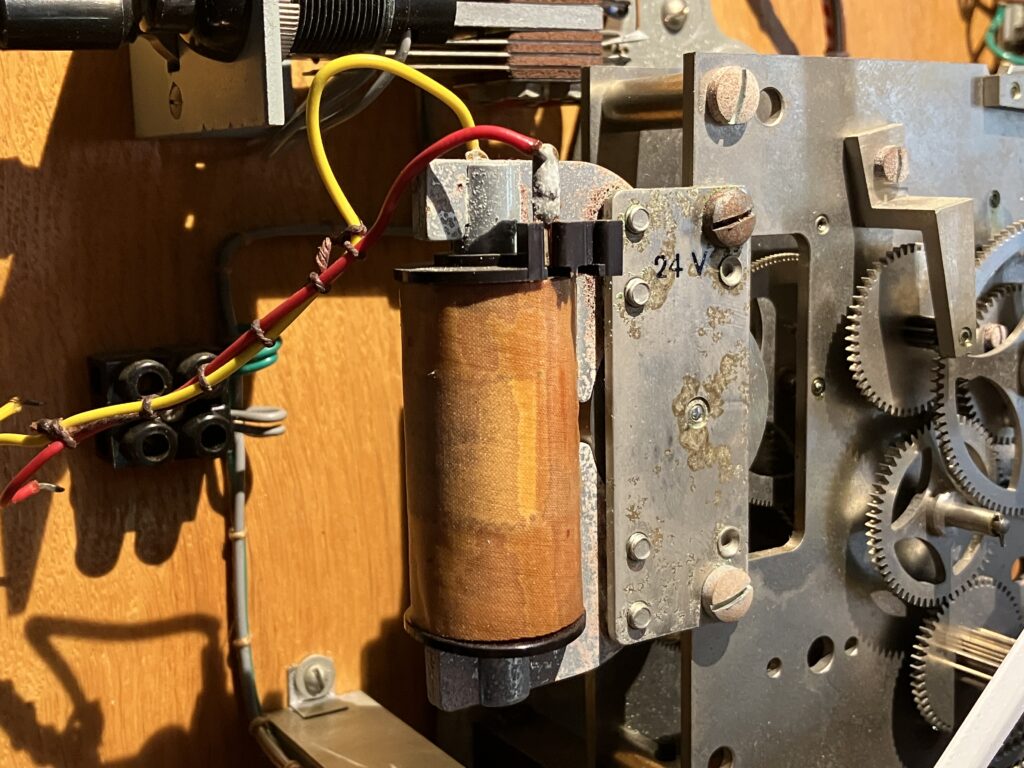
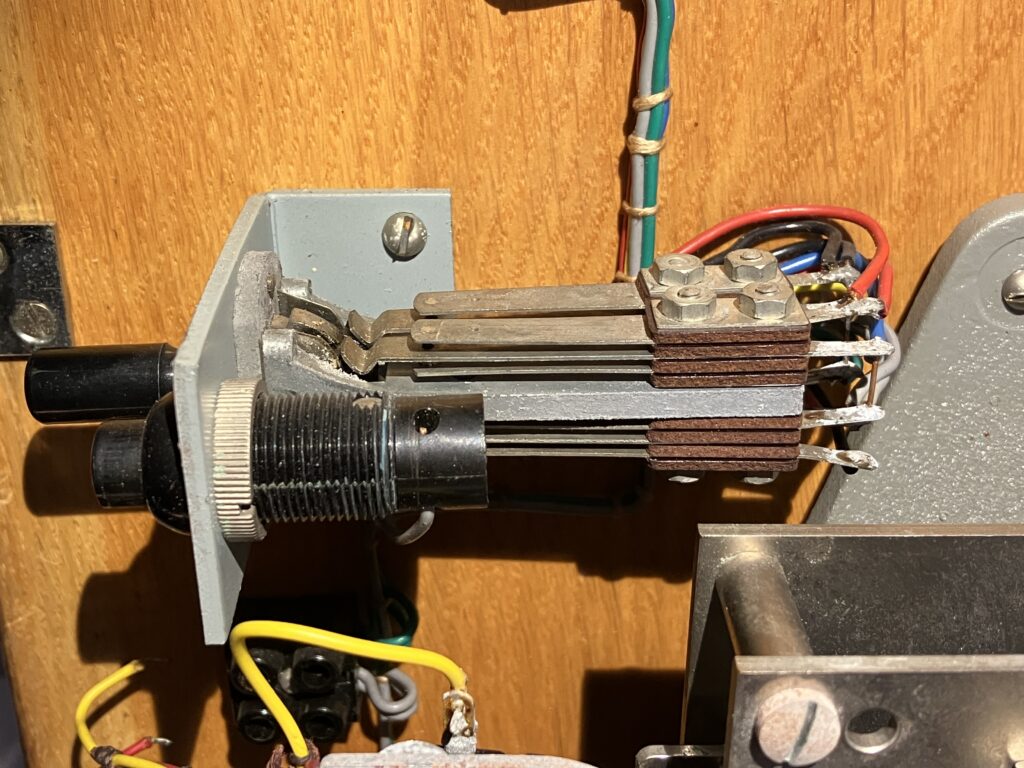
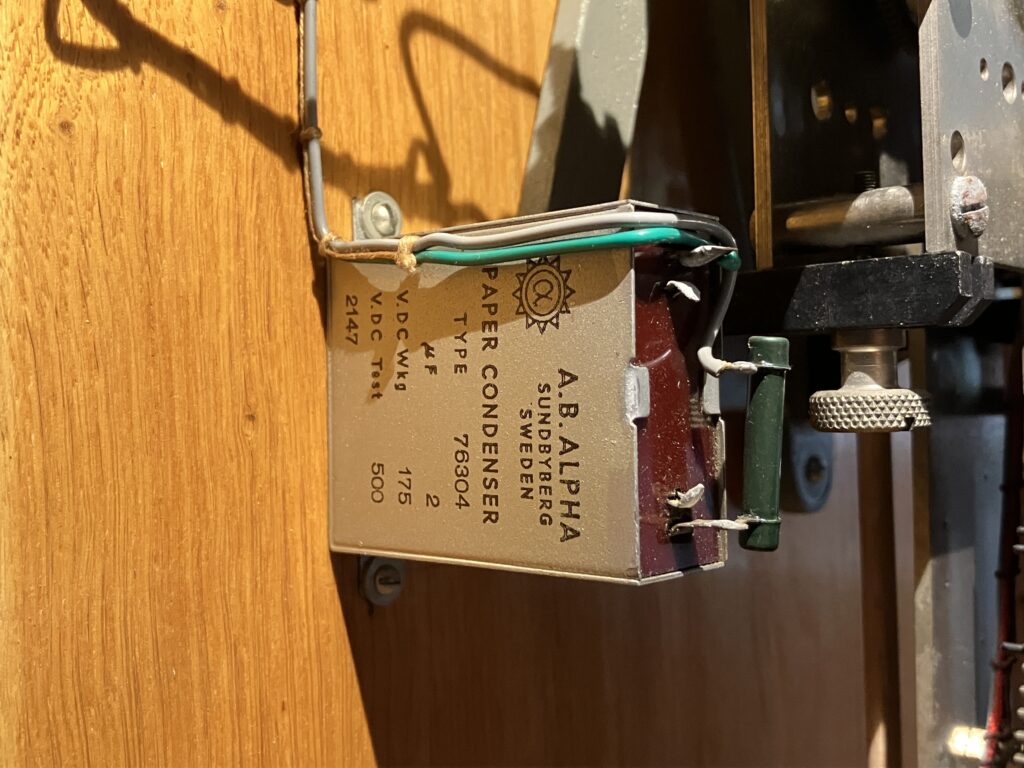
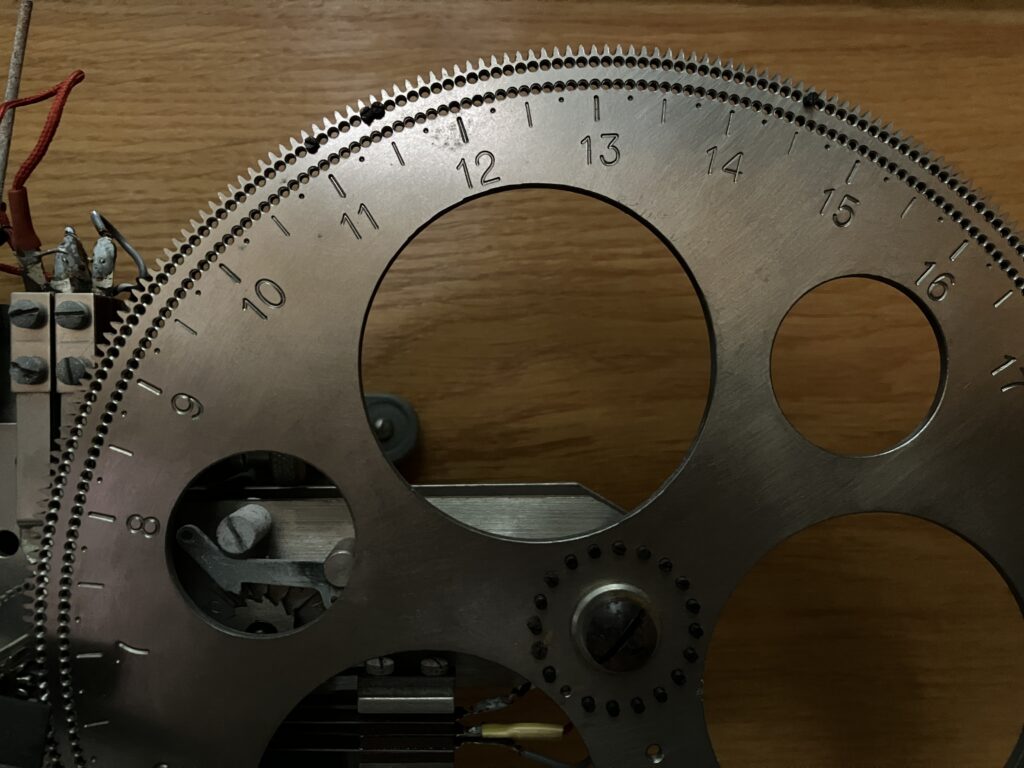
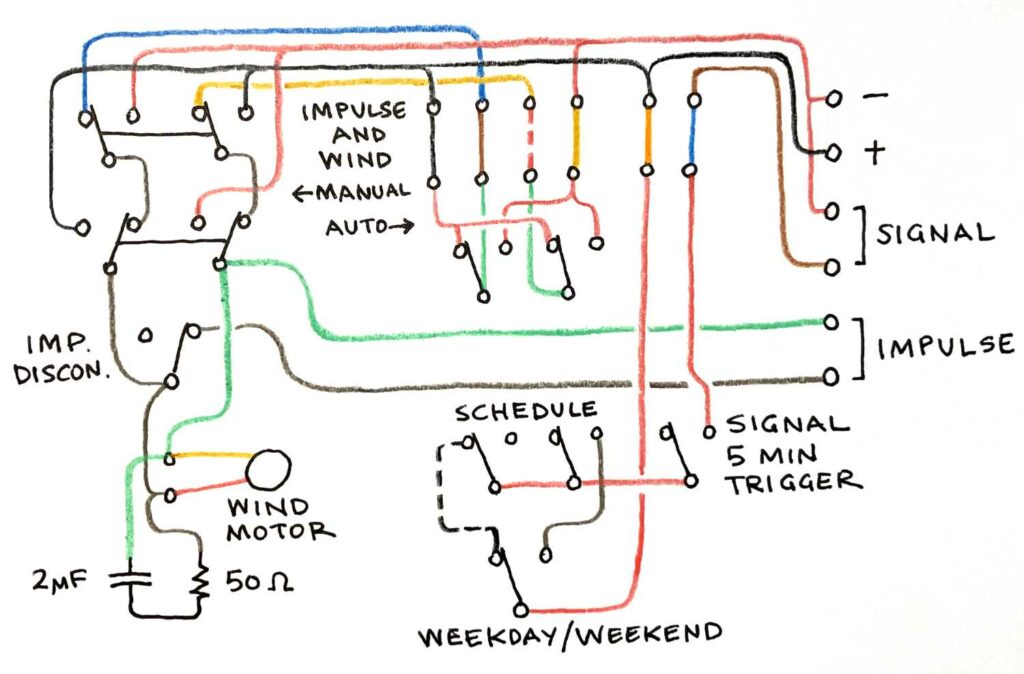
New pendulum
I decided to fabricate a new pendulum first, to seek signs of life. The suspension spring was bent but present; enough to get on with. I used a 1/4” dowel for the rod, an upside-down furniture leg for the bob, and a 3D-printed hook. The clock accepted it eagerly and, even without a service, began ticking away happily.
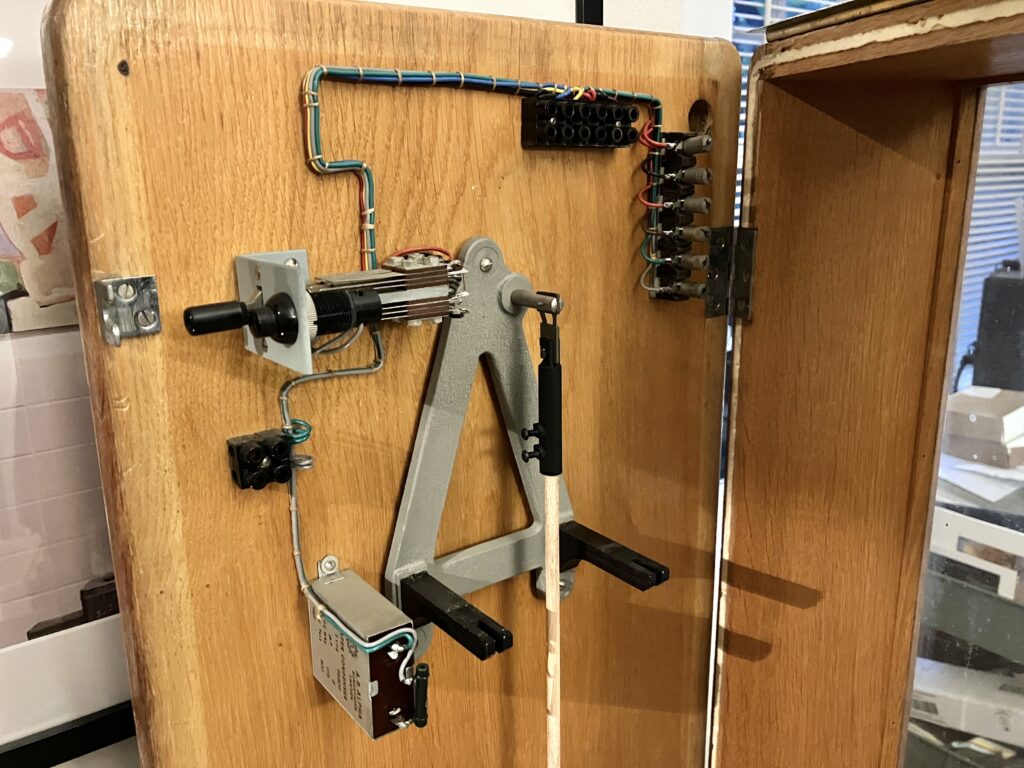
Disassembly and service
Disassembly demanded a fair bit of patience and penetrating oil, as most of the fasteners had oxidized in place.
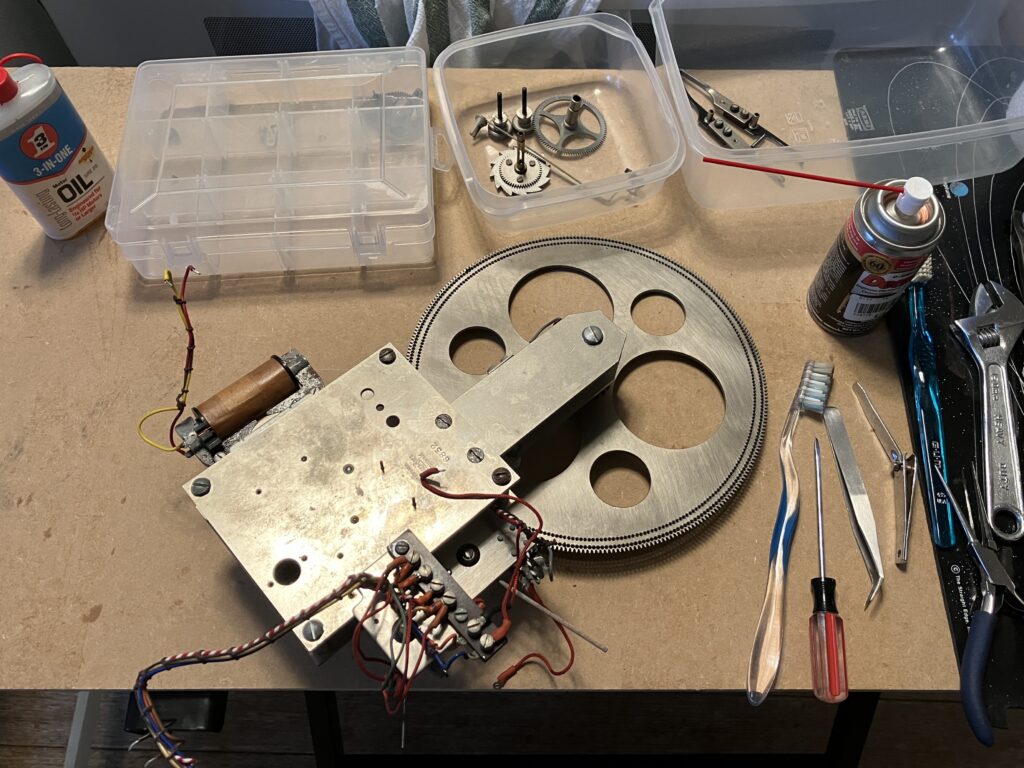
It demanded careful organization, too – especially for the switches, which are composed of several layers of contacts and insulators and must be reassembled in exactly the right order.
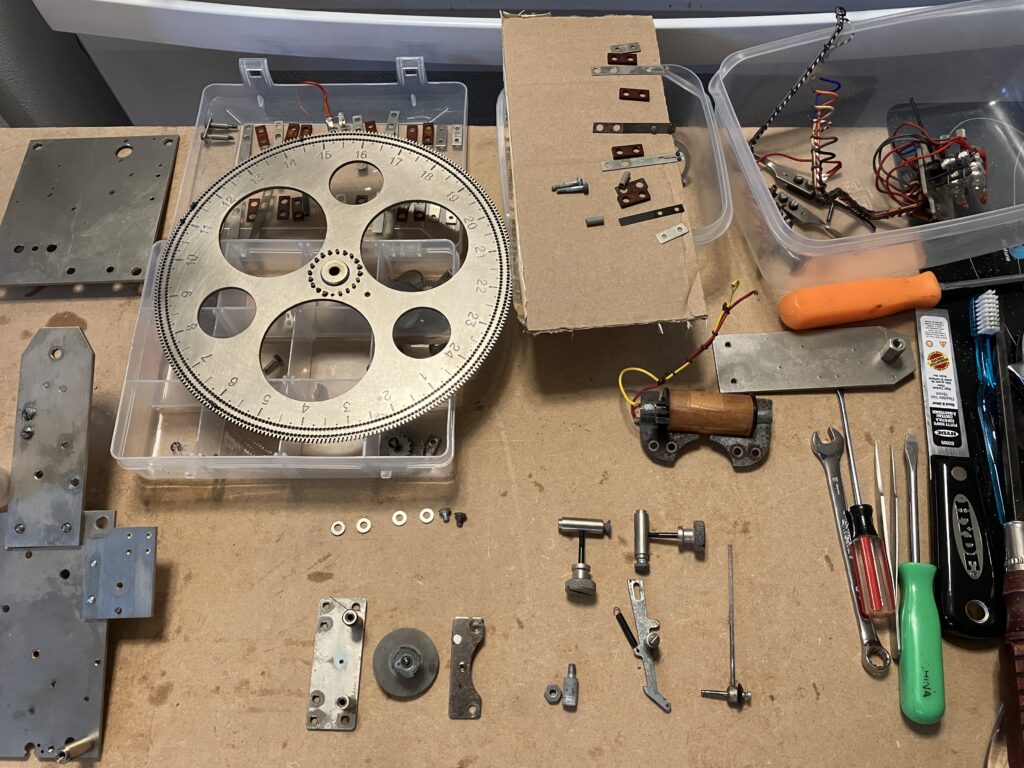
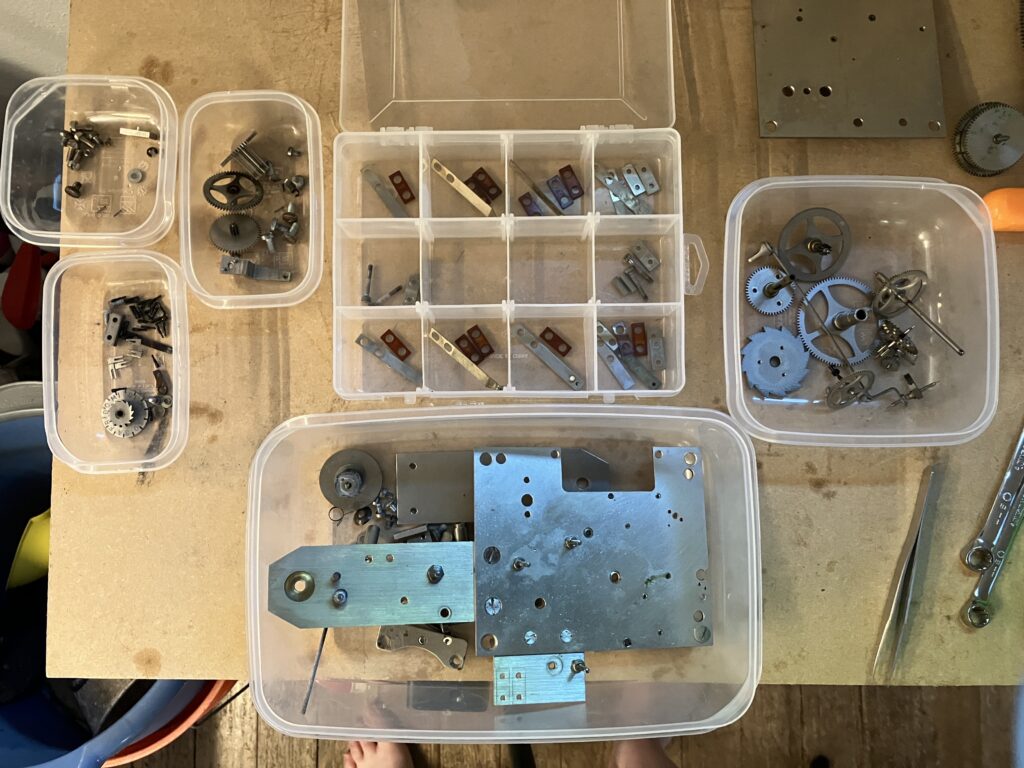
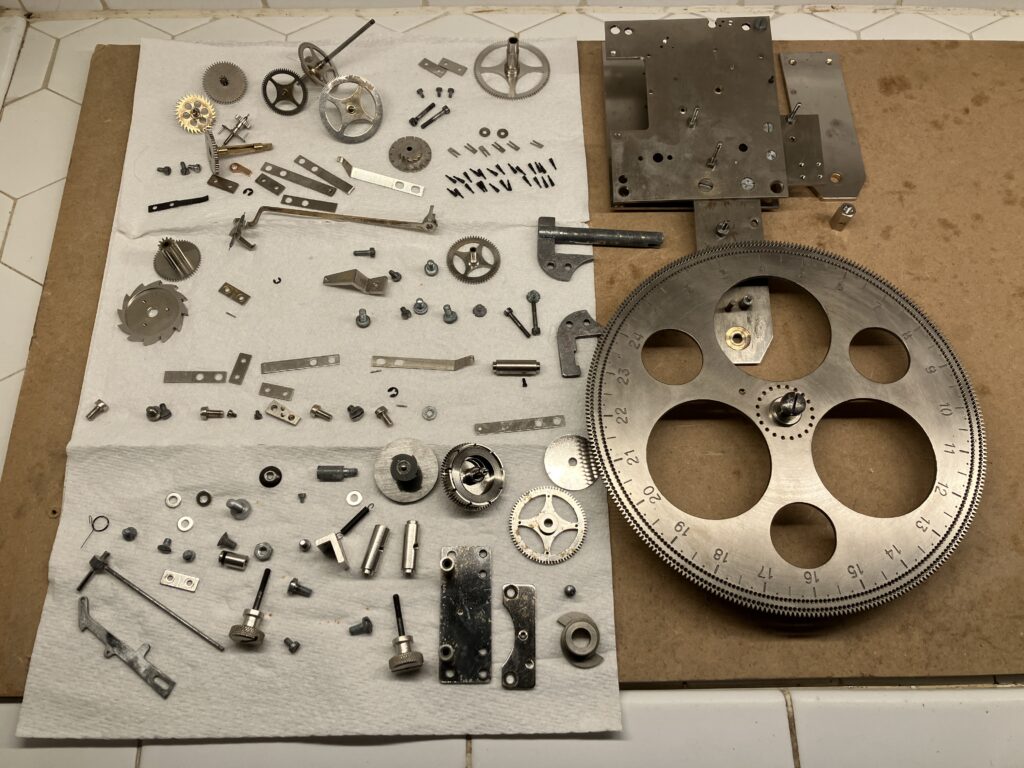
Electrical safety
In the meantime, I sought the advice of experts on the NAWCC forums on how to handle the electricals (as well as whether there might be asbestos present – which there isn’t). One gentleman kindly advised me the paper capacitor was probably bad. Since I have an LCR meter, I was able to indulge his interest – and we determined that, indeed, it was liable to go explody if powered up.
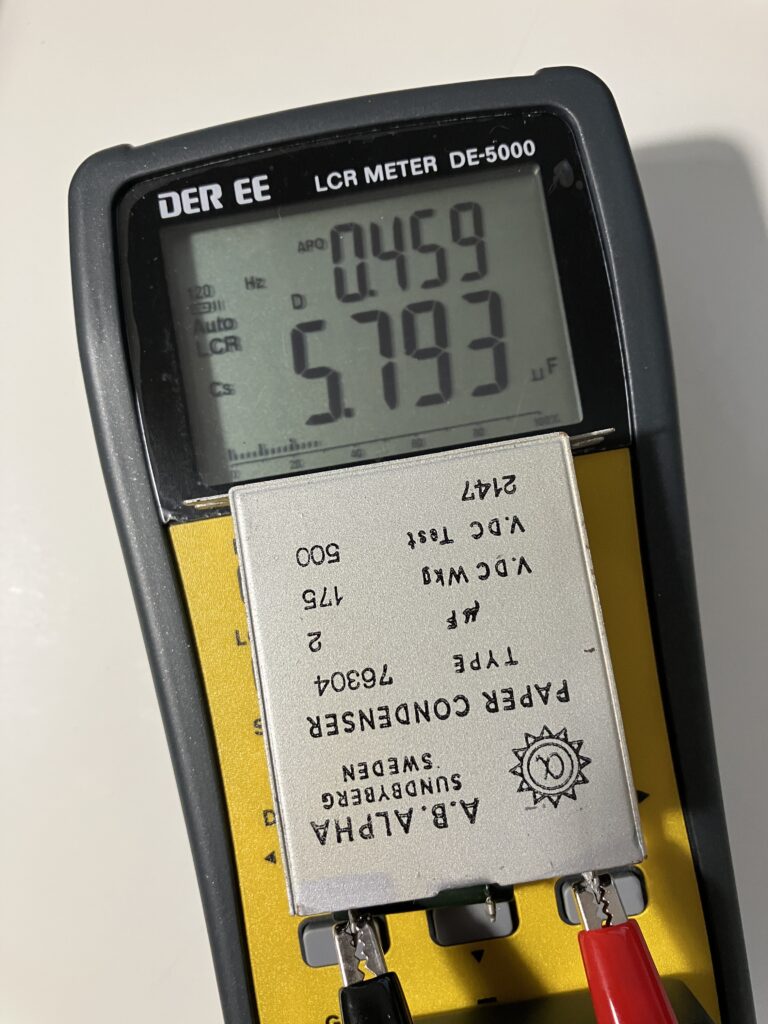
Fortunately it’s inert if left unpowered – so I decided to leave it (and its matching 50Ω wire-wound resistor) in place for originality, and attach modern components to the side. I couldn’t find a black Euro-style terminal block to match the clock’s existing ones, so I bought a white one and transplanted its hardware into a 3D-printed black one.
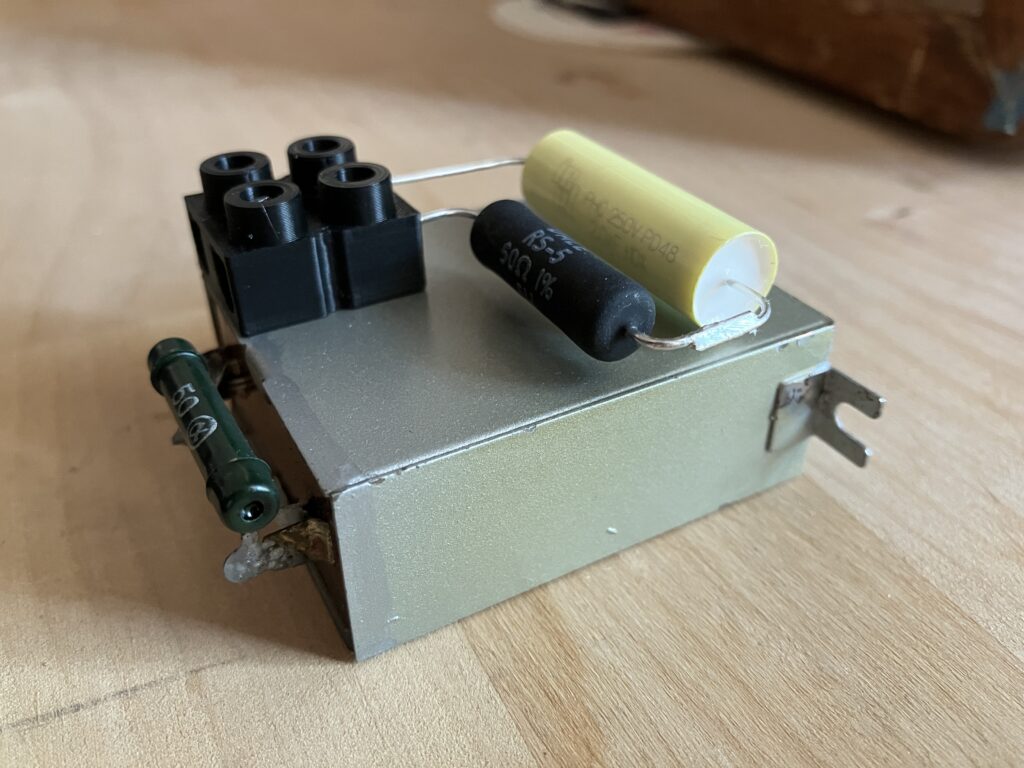
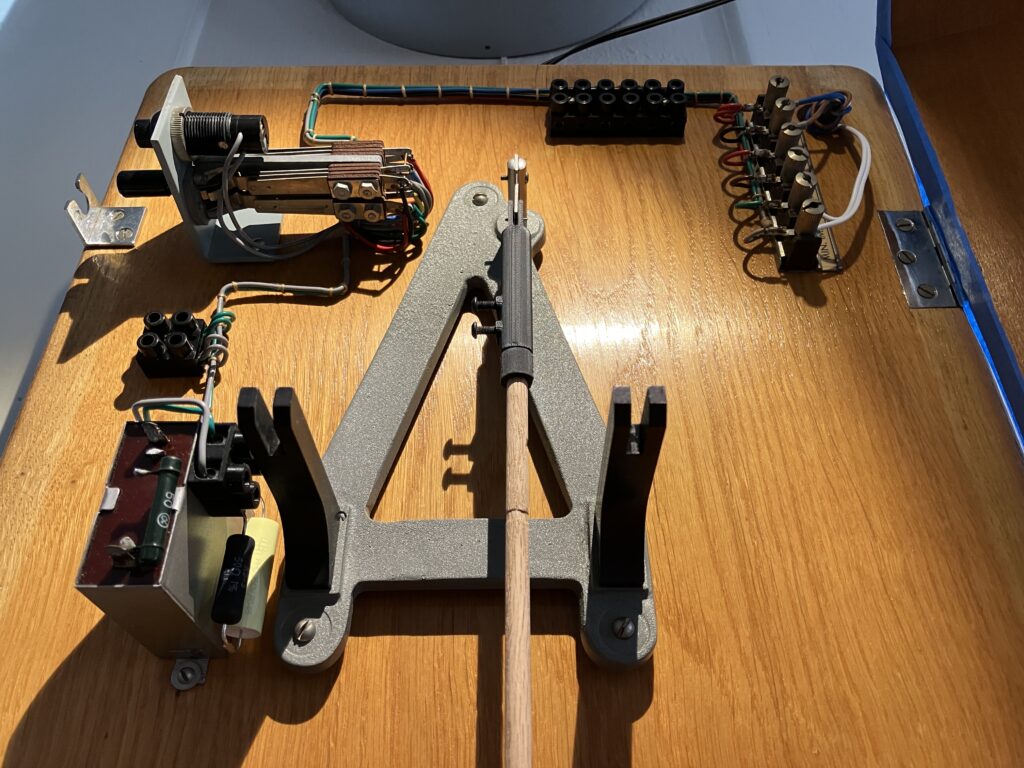
New dial
To showcase the clock’s mechanism, I decided to fabricate a transparent skeleton dial – and rather than copy the original dial exactly, I decided to imitate the pilot dial from a matching Ericsson punch clock from the same period – no less utilitarian, but with a bit more visual interest (and there is precedent for a similar design in other Ericsson master clocks).
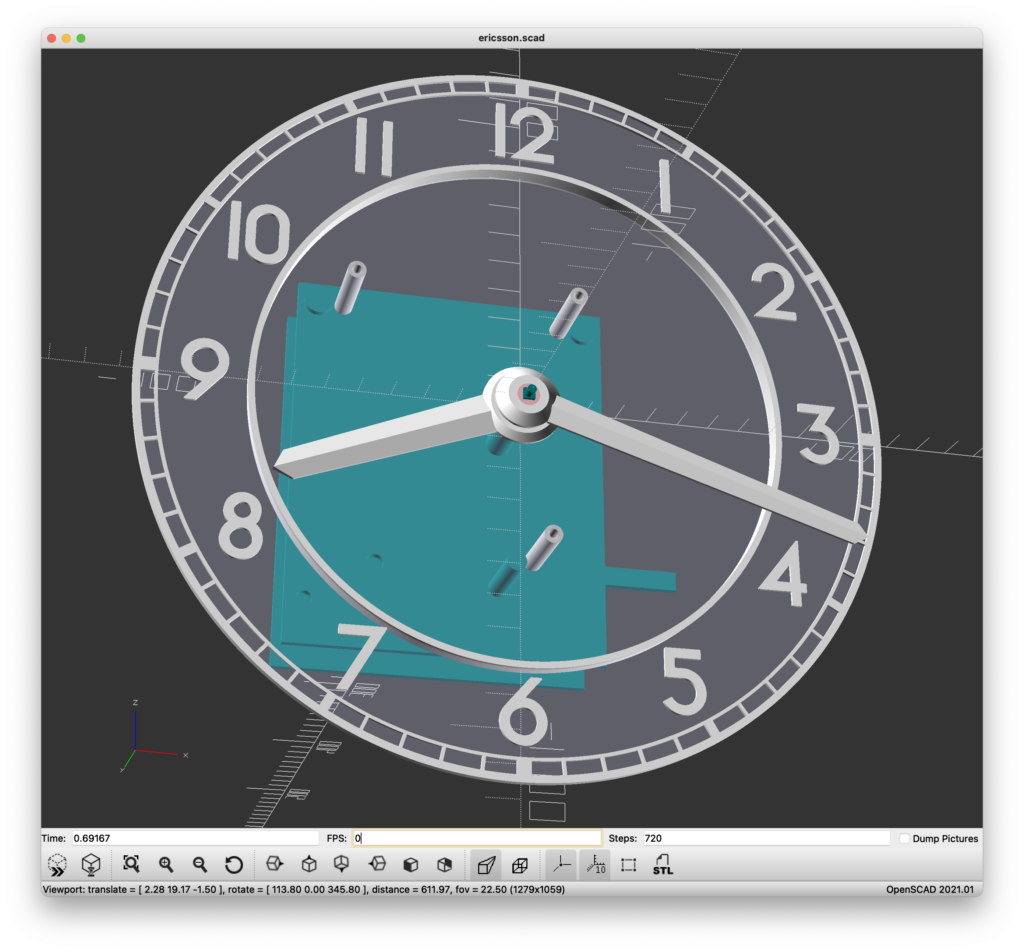
I settled on a design made of two pieces of acrylic and 3D-printed legends, standoffs, and hands, assembled with superglue and M3 screws. The double-level design adds more visual interest and improves readability since it brings the tick marks closer to the minute hand. The acrylic was cut by SendCutSend (who included – fittingly enough – Swedish Fish).
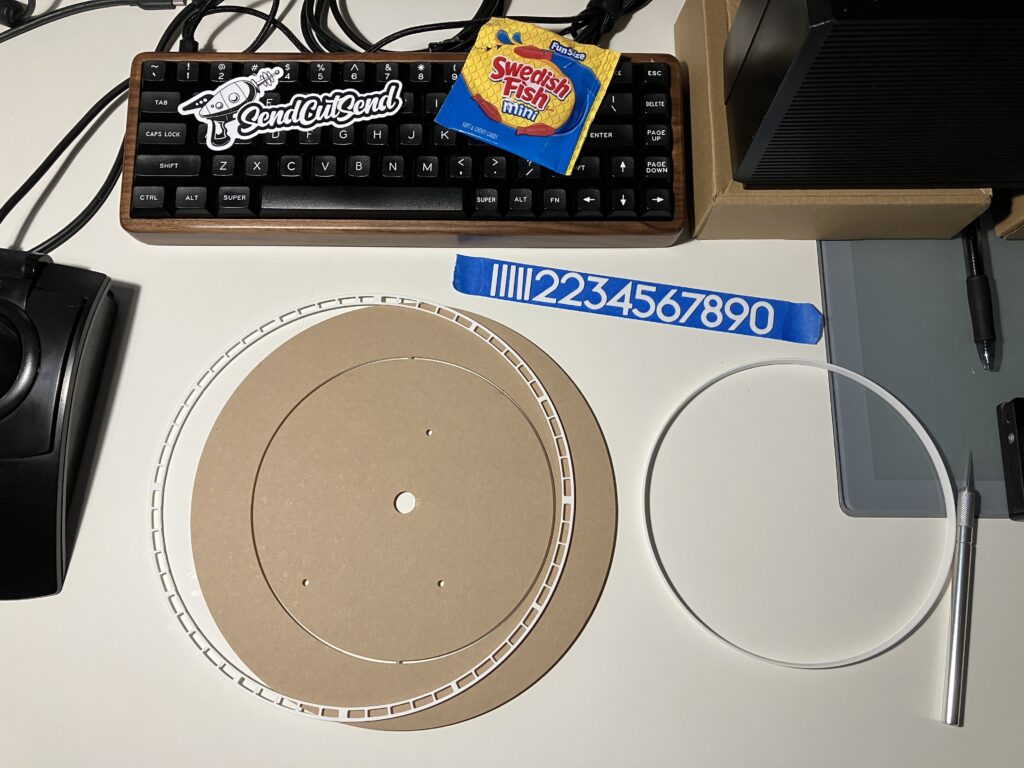
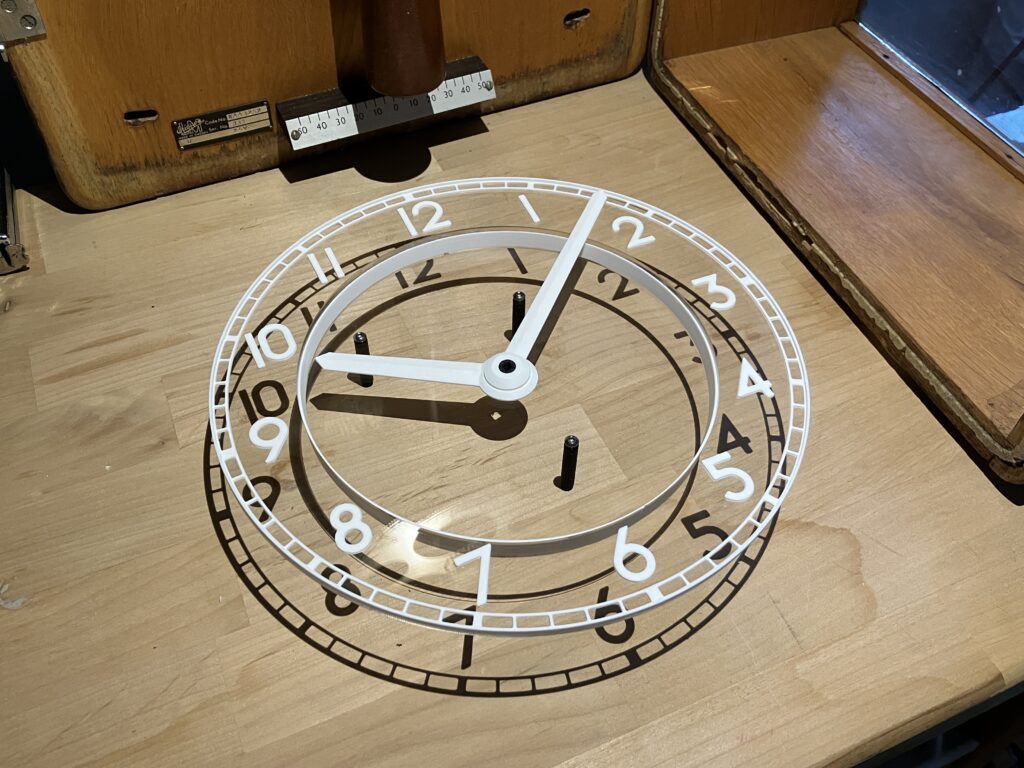
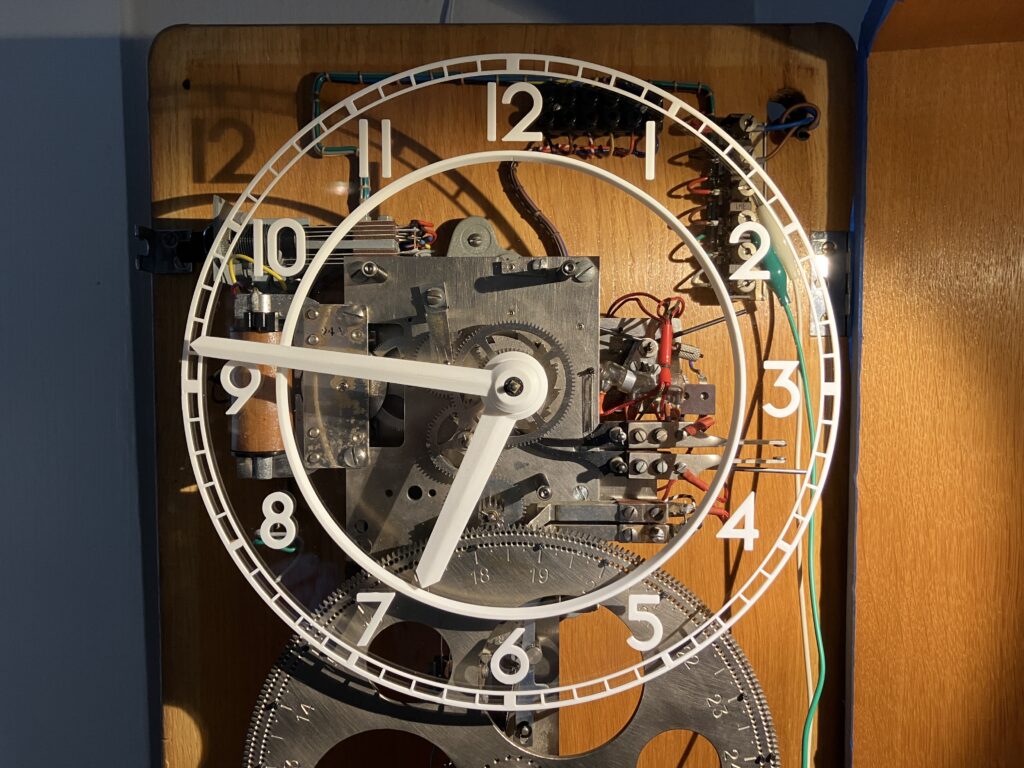
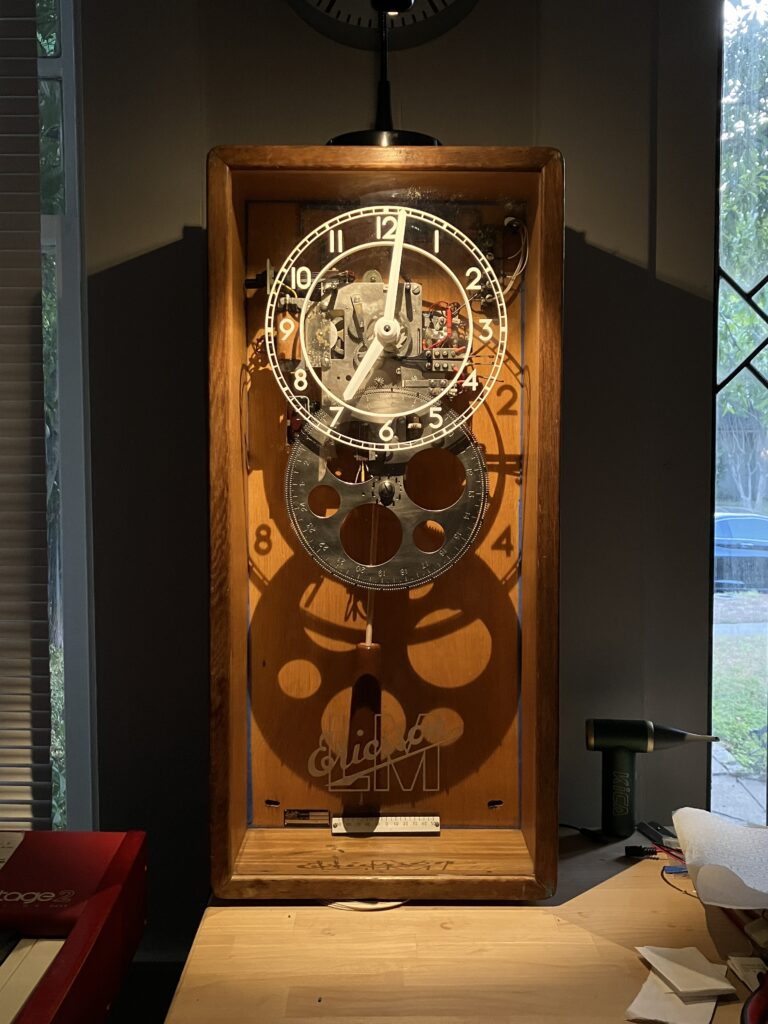
All in all, a fortuitous piece for my first vintage master clock. It will appear again on this site, since I plan to use it as a test bed for some other development projects.